Altium Board Slots
The footprint on the left in this image clearly leaves much more empty space around the component leads, where the image on the right provides a snug fit. This makes the circular hole configuration much more prone to common PCB Assembly defects such as solder joint voiding, since more solder is required to fill the holes.
Altium Designer is one of the most popular and frequently used CAD software for schematic design and PCB Layout. If you are planning to become a professional hardware design engineer, if you are moving to Altium Designer from different software or if you have never designed any board before and you would like to learn it, this course will help you. To facilitate safe patient transfers, care givers have more control and require less lifting thereby reducing the potential for falling or injury Features comfortably shaped hand holes placed near the ends, providing a firm grip with the greatest amount of leverage Suitable and versatile for a wide variety of transfer applications from the wheelchair to a bed, car, chair, and more Made from. Re: How to define milling slot in altium michaelkellett May 10, 2015 4:08 AM ( in response to greenben214 ) I sound like a broken record here but the OP really MUST talk to the board manufacturer. Altium Board Slots, aqua casino boston, poker 480x320, holdem la leyenda. (slots are 2mm - default milling bit size, with tabs with 5-hole perfs). I realize the board house will most likely want just the path for the router and not its actual shape, but I want to create gerbers with the routed slots so there's no confusion about inside vs. As well as I like having the 3D view look like what I expect to get.
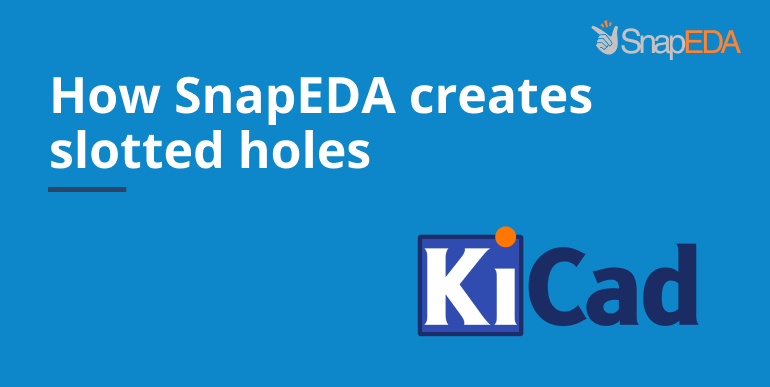

These concerns become more significant as the size of the pins increases, from both design and production perspectives, so large blade-style connectors should definitely use plated slots rather than circular holes. At Bittele, we can still work with circular holes for rectangular pins when the part is relatively small, such as the standard barrel power connector used in this example. That being said, the circular holes do also take up more space on the PCB itself, and using plated slots can often help in size-restricted designs.
For the design of non-circular holes, a few things must be considered, but the process is fairly straightforward overall. It should first be noted that slots can be defined as plated through holes (PTH) or non-plated through-holes (NPTH). PTH slots are most often used in component footprints, and most PCB layout CAD programs provide an option in their footprint editor to define a hole as circular or oval. This will be enough for Bittele’s PCB Fabrication team to recognize the hole and use the correct process, but for extra clarity, some clients also indicate slot holes on a fabrication layer of their Gerber files.
NPTH Slots can be designed in the same manner, and simply designated as NPTH / Mechanical in the CAD software, or they can be designed on the Board Outline Gerber layer. The following images show multiple options for both PTH and NPTH slots, first in a Gerber file view and then a 3D rendering of the resulting board.


Altium Board Slot
Related Articles:Search articles:
Although it’s one of the most popular PCB design tools, Eagle doesn’t have a native way of defining plated slots. Luckily, there are methods of getting fully supported slots in Eagle!
SnapEDA follows Eagle’s official method when defining slotted holes. This method is ideal for 2 layer boards. Please note though that if your board has many layers, and some are internal copper layers, that you’ll need to isolate the slot from them manually to avoid short circuits. Alternatively, you could also create the slots in the dimension layer instead of the milling layer. You can see our FAQ on slotted holes in Eagle here.
If you are uploading your zipped Gerber files to OshPark, you should pay close attention to your slotted holes. OshPark only applies guarantees to slots indicated on the drill layer. Drawing slots on the outline layer usually works, but doesn’t generate guarantees.
So, if, after processing, you don’t see the drill slots in the output files while verifying your design, please re-design your library by following the method described below.
1. Place two vias where the slot starts and ends.
2. Set the drill size of the pad to the desired slot width.
3. Draw a line between the center of each via on the Milling layer using the line tool.
4. The line width must be equal to the desired slot width.
5. Draw two more lines between the via centers on the top and bottom layers.
6. The width of these two lines would be your pad diameter size, but at minimum must be (slot width) + 2*(annular ring)
.
7. Next, draw two more lines between the via centers on tStop and bStop.
8. The width of these lines should be the same as the copper, or, you can make them up to 4mil (0.1016mm) wider to account for mask expansion.
Note: For 4 layer boards, it’s recommended to draw 2 additional lines on the internal layers to connect traces.
According to OshPark, the official recommendation from Eagle works many times, so it’s not required to redo parts. But it’s not guaranteed, just like other outline methods, which is why it’s always a good idea to double check.
There are many ways to draw slots in Eagle. The most important thing is to make sure that your PCB manufacturer is interpreting them correctly, and that the file is correctly defining the slot size, shape, and location for your particular design!
Happy designing!